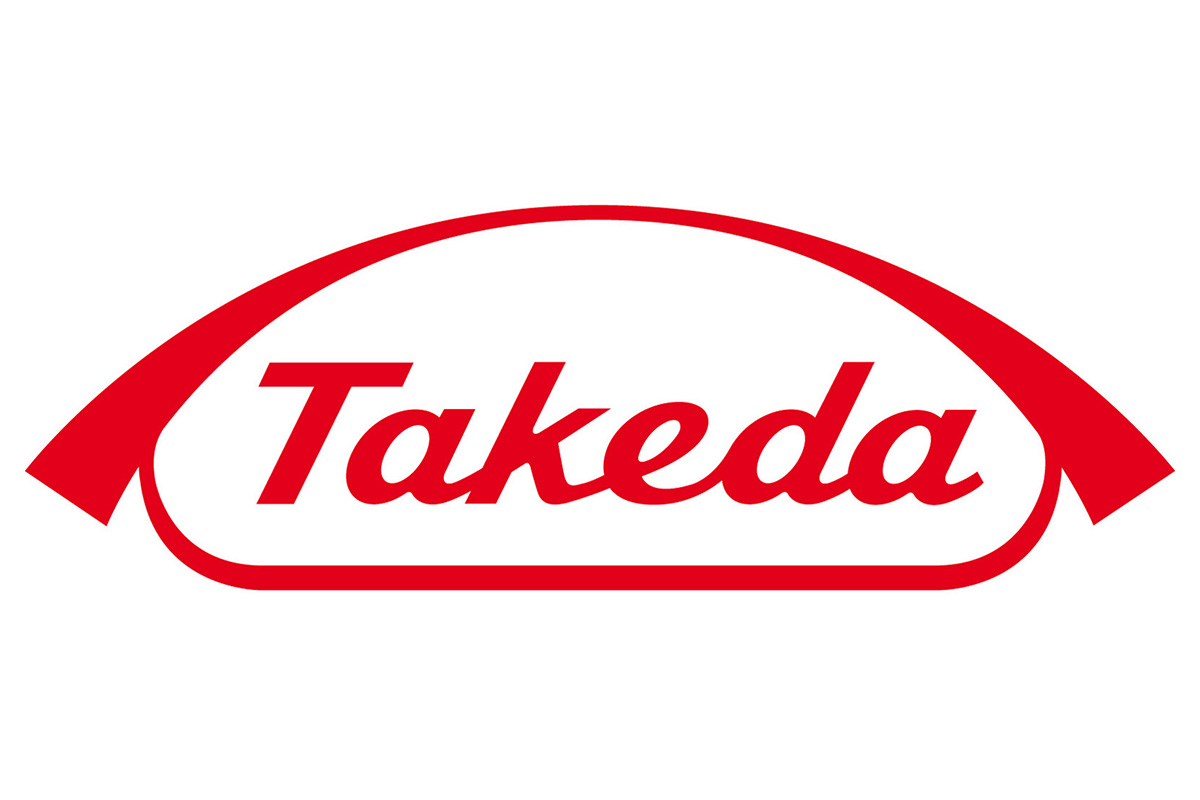
COVID-19 Testimonial Series | Takeda Neuchâtel Manufacturing Site

Share this article
Reorganisation of teams and work streams to ensure the production and delivery of life-saving products while protecting the health of 650 employees
The following article is part of BioAlps’ testimonial series and was written by Mr Juergen Wagner Head of Takeda Neuchâtel Manufacturing Site. Our series aims to provide a platform for the different life sciences actors from western Switzerland, who are active in finding and developing solutions to fight against the new coronavirus, to share their experience.
Presentation of Takeda’s COVID-19 related activities
In Neuchâtel, we produce two life-saving therapies to treat hemophilia A and Von Willebrand disease. Our manufacturing site has continued its production during the pandemic.
At a global level, Takeda is engaged in the global efforts to address COVID through two main areas:
CoVIg-19 Plasma Alliance | Takeda is co-founding member of the CoVIg-19 Plasma Alliance. Eight additional biopharma companies and other partners have joined this alliance. The CoVIg-19 Plasma Alliance is an unprecedented partnership of the world’s leading plasma companies, spanning plasma collection, development, production, and distribution. Rather than pursuing our individual research, we are putting public and patient health first by working together. Our goals are to accelerate the development of a potential treatment, improve our chances of success, and increase supply of the potential treatment.
COVID R&D Alliance | This alliance is focused on finding treatments through shared expertise, data, and evaluation of drug candidates. The COVID R&D Alliance brings together the world’s most experienced and accomplished leaders in therapeutic drug research and development to identify, study, and accelerate the most promising candidates across a broad spectrum of therapies and vaccines.
Exogenous impact of COVID-19 on the company
In Neuchâtel, our biotech manufacturing site is running 24/7. Our core priorities were to ensure both the supply of our life-saving products to our patients in 80 national markets worldwide, while protecting the health of our 650 employees. To do so, we kept essential minimal teams onsite to ensure the production while ‘sending home’ all remaining teams. Half of our 650 employees had to switch to remote home-office overnight, the other half continued to operate onsite with protective measures.
We reacted fast. We adopted our first COVID measures as of 2nd March 2020, two weeks before the Swiss federal government imposed the lockdown. We started by tracing the recent travels of employees from countries considered at risk at that time, namely Italy in the first instance. Over the weeks, we applied a large range of measures, such as ensuring physical distance in common areas, offices, and our restaurant, as well as renting rooms in town to facilitate the mobility of our commuters who operated onsite.
Similar to other companies, we switched to virtual meetings where possible, managed the whole site at a distance through intensive communications, and developed new streams of work imposed by the switch to a massive and immediate remote home-office framework for many employees. Along the way, we have developed skills and competences to manage remote home-office adequately.
Reducing risks of virus spreading. We also introduced very early measures to reduce the risk of the virus spreading amongst colleagues. We modified shift schedules and work flows to reduce the need or the possibility for large groups of employees to meet face-to-face. Wearing a mask was mandatory in all our meeting rooms as of June, and we are about to make it mandatory in our cafeteria and any other shared spaces where sufficient distance cannot be ensured. Such measures aim at avoiding – or keeping potential infections localised and small among our employees.
We succeeded. Our production ran continuously to date without supply interruptions. We succeeded in preventing the propagation of the virus onsite. As of 2nd March, we asked all employees showing potential symptoms or who had been in contact with potential cases to stay at home.
Our success has been possible thanks to the engagement, agility, resilience and professional responsibility of our teams, our management and our ‘Covid Task Force’.
As such, COVID-19 had no impact on the products we manufacture in Neuchâtel, but a strong and immediate impact on the reorganisation of our teams and work streams, between remote home-office vs. onsite operations.
More about the Takeda Neuchâtel Manufacturing Site and its activities
Endogenous impact of COVID-19 on the company
We are learning a lot through this unprecedented experience. Some changes have shown highly positive aspects that we will keep and adapt for a long-term perspective. Virtual meetings have proven to be effective. They also enable a higher attendance than face-to-face. Remote home-office is another important “discovery” for an industrial site like ours. The reality has shown that it is possible for many employees – even for a production plant – and brings clear added-value. But all of this needs to be adapted and managed within a long-term perspective. We are now working on structuring it with due policies, skills development and guidelines to keep it sustainable. As evidence of our engagement to our employees, we provided them all with a special financial allowance so that hey can install an ergonomic desk at home to meet both security and well-being standards.
Cantonal and Federal support measures | Takeda’s feedback
We did not ask for any financial support from the authorities, nor did we apply any reduction of work time. However, we established direct communication lines with cantonal and federal services. At canton level mainly with the Health and Economy services. We asked and established with the Service of the Economy of the Canton of Neuchâtel for a weekly information exchange together with other peers from the biopharma industry. At national level, we interacted with services such as the Federal Customs Office regarding the transit of our colleagues living in France or with Interpharma acting as liaison between authorities and the Swiss Pharma Industry.